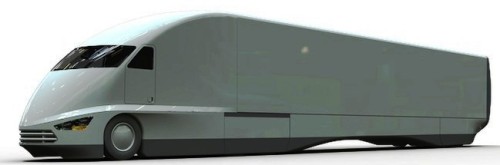
A potência necessária à propulsão de um veículo é dividida em duas parcelas principais, alem da resistência em rampas:
– Potência para vencer a resistência ao rolamento das rodas
– Potência para vencer a resistência à penetração no ar
A resistência ao rolamento depende, basicamente, do peso do veículo e do coeficiente de atrito de rolagem entre o pneu e o solo.
O atrito de rolagem pode ser otimizado agindo-se no composto, na estrutura e na pressão de trabalho dos pneus. Os chamados pneus “verdes”, com sílica incorporada, têm apresentado bons resultados, principalmente quando associado à rigidez do pneu, suas características construtivas e pressão de trabalho, diminuindo suas perdas por deformação. A potência para vencer a resistência ao rolamento é praticamente linear com a velocidade do veículo.
A resistência aerodinâmica esta diretamente ligada à forma do veículo ou seja, do seu coeficiente de arrasto (Cx) e de sua área frontal. Quanto menor o produto destes dois fatores, tanto menor será a sua resistência à penetração no ar. A potência aerodinâmica cresce com o cubo da velocidade, significando que para duplicar a velocidade do veículo a parcela de arrasto produzida pelo ar somente poderá ser vencida com uma potência 8 vezes maior (2³, dois elevado ao cubo).
Os carros hoje em dia já estão bem otimizados com relação ao seu formato aerodinâmico, tanto é que a maioria das marcas estão ficando muito parecidas uma com as outras, sendo difícil identificá-las ao primeiro olhar.
Particularmente os caminhões, objeto desta matéria, são mais complicados em sua otimização em termos de rolamento e aerodinâmica. É muito fácil entender esta dificuldade, pois os caminhões são muito mais pesados que os carros e suas áreas frontais também são muito maiores. Os coeficiente de arrasto aerodinâmico enormes, em média entre 0,9 e 1,0, dificultam ainda mais o processo.
Diminuir o peso dos caminhões é uma tarefa muito difícil, pois envolve compromissos de resistência mecânica do chassis necessários para resistir à carga útil a ser transportada, normalmente maior que três vezes o peso próprio do caminhão.
Diminuir o coeficiente de atrito de rolamento com a utilização de pneus “verdes” com sílica incorporada está cada vez mais freqüente, reduzindo a resistência à rolagem em torno de 8 a 10%. No entanto, o compromisso de sua durabilidade para o uso severo é ainda um ponto a ser melhorado, como também o seu maior custo, que tem sido um ponto inibidor ao seu uso.
Diminuir a área frontal do caminhão também não é tarefa fácil, pois o tamanho do implemento (carroceria tipo baú, carga aberta etc) está ligado diretamente ao volume da carga a ser transportada.
Diminuir o coeficiente de arrasto aerodinâmico, tarefa também difícil, é o que as fábricas de caminhões e implementos têm investigado ao longo dos anos.
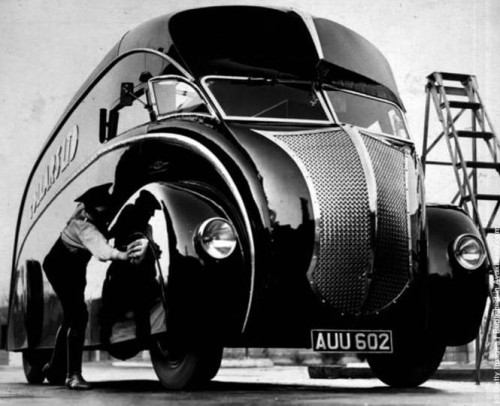
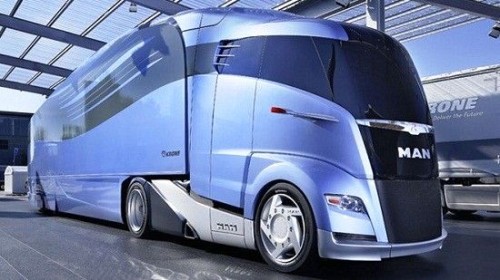
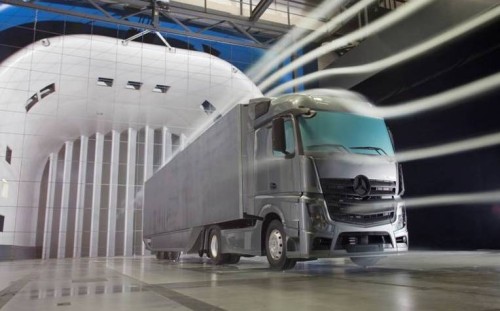
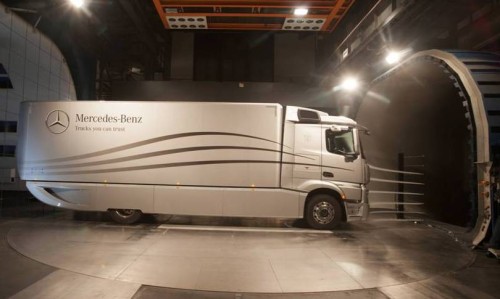
A grande dificuldade prática é que os implementos normalmente não são feitos pelas fábricas de caminhões e também não são estandardizados em suas dimensões e forma, virando cada caso é um caso para o trabalho de otimização aerodinâmica. Imagine adotar ações como defletores do teto, arredondamento do baú, defletores laterais, distância entre o baú e a cabine individualmente. Torna-se realmente muito difícil.
A saída seria formar parcerias entre as fábricas de caminhões e de implementos, além de contar também com organizações governamentais para estabelecer normas (standards) que regulassem a sua fabricação.
Para dar uma exemplo prático de como a aerodinâmica pode ajudar muito na economia de combustível, volto à década de 1980, quando a crise mundial do petróleo estava a todo vapor e os custos dos combustíveis, nas alturas.
A Ford, em parceria com o Centro Técnico Aeroespacial (CTA) em São José dos Campos (SP), começou a desenvolver a aerodinâmica de seus veículos em túnel de vento. Lá foram testados o Corcel II, a Pampa e outros veículos-conceito como, por exemplo, o substituto do Del Rey. Foram realizados também estudos na área de caminhões.
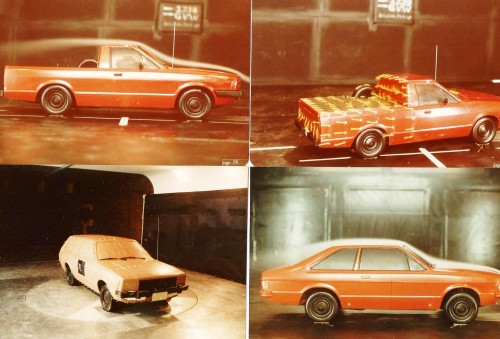
Em 1981 um modelo em escala 1:5 do caminhão Ford F-19000 configuração tipo baú (cargo van) foi testado no túnel de vento do CTA.
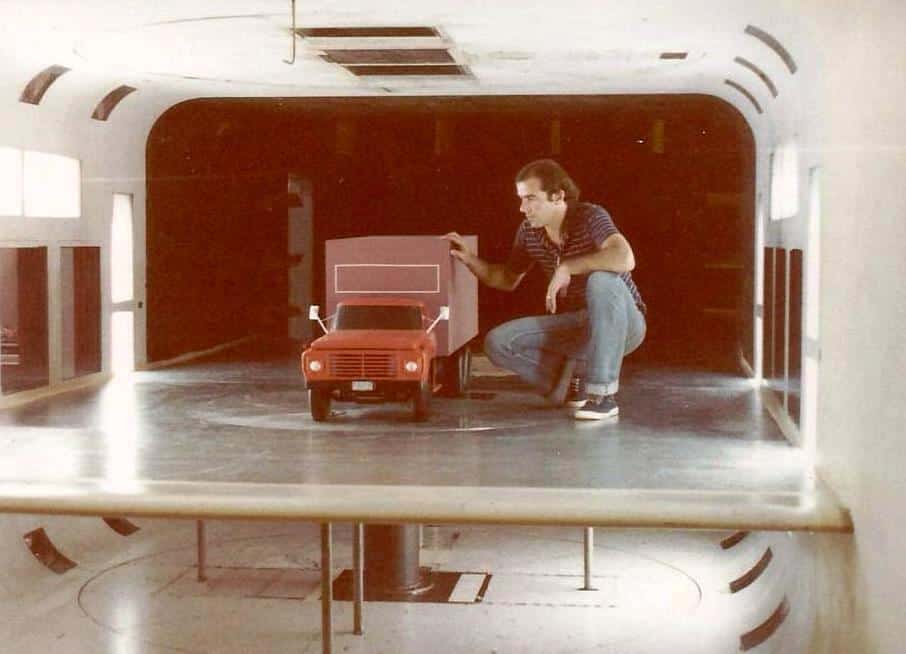
O resultado dos trabalhos foi uma redução de 32% no coeficiente de arrasto conseguido através de uma carenagem (spoiler) instalada no teto da cabine, defletores laterais, arredondamento dos cantos dianteiros do baú, defletor abaixo do pára-choque dianteiro, defletores no baú na área das rodas, entre outros. Passamos de Cx 0,925 da configuração original para 0,625 na configuração otimizada.
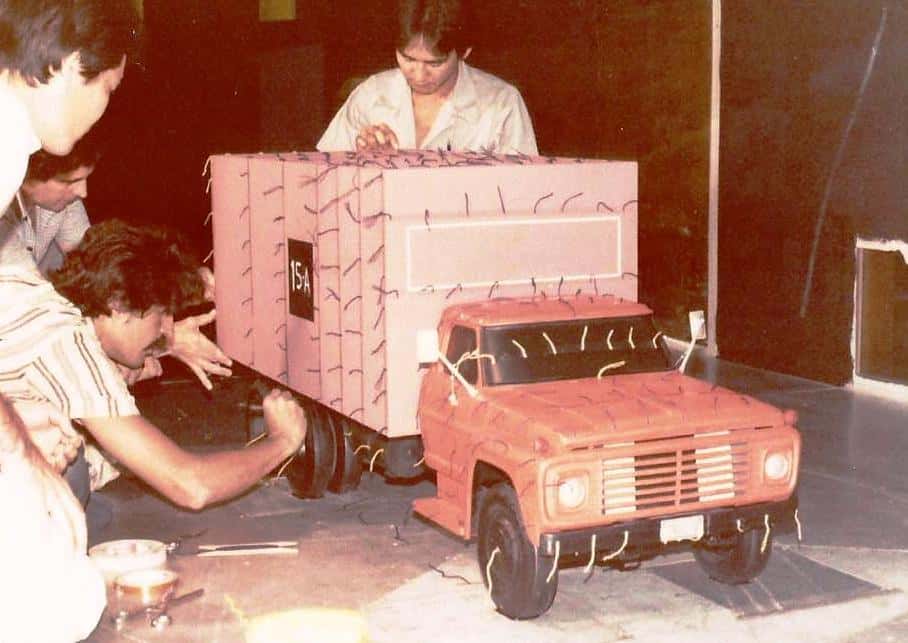
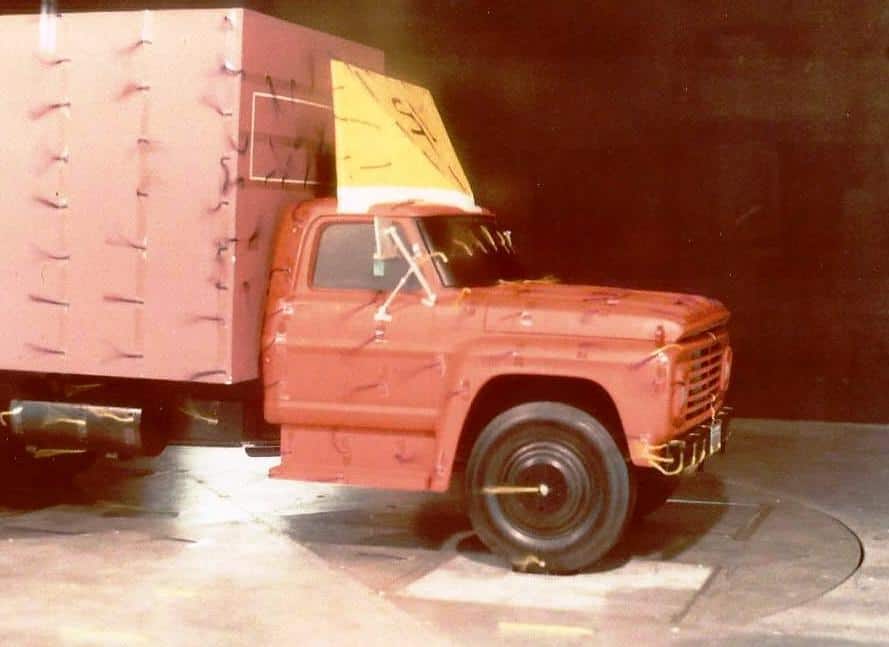
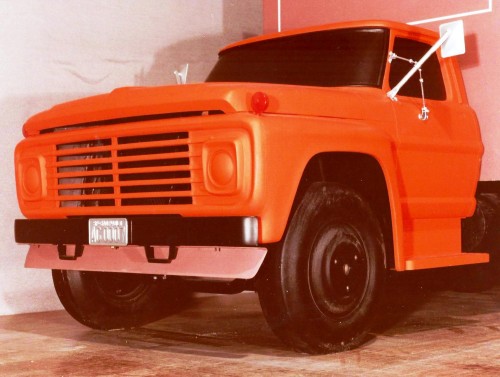
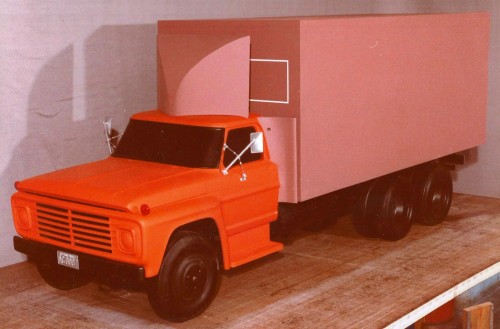
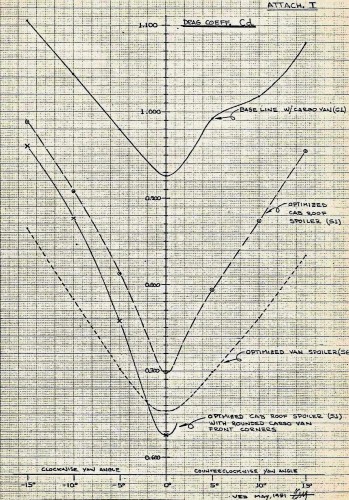
Com a redução do coeficiente de arrasto aerodinâmico, a potência resistiva diminuiu 30 cv, resultando um consumo de combustível 8% menor em testes comparativos reais na estrada.
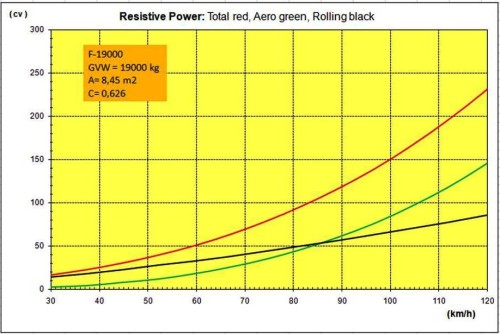
Fico imaginando o consumo anual de 60 bilhões de litros de óleo diesel no Brasil. Uma diminuição de 8% significaria uma economia de quase 5 bilhões de litros, o que é realmente muito significativo.
Valeria realmente a pena fazer um estudo de negócio, empreitada esta obviamente a ser liderada pelo governo brasileiro, incentivando as parcerias entre os fabricantes de caminhões e implementos para pôr em prática, em nível nacional, o que hoje é feito individualmente por migalhas. Caberia até uma legislação com normas técnicas pertinentes para o caso.
CM
Créditos das fotos e ilustrações: arquivo pessoal do autor, www.mercedes-benz.com.br, www.pinterest.com, www.xepro.vn, www.wired.com