As fábricas de automóveis. ao longo dos anos, vão ficando conhecidas no meio consumidor por suas características marcantes. Citando alguns exemplos, o bom acabamento dos carros da Ford, a robustez dos Volkswagen, o compromisso conservador da General Motors, a esportividade dos Porsche, entre outros.
Se eu perguntar ao leitor como você se posiciona a respeito dos carros Mercedes-Benz, sem medo de errar a resposta será a de que são luxuosos e de acabamento primoroso em todos os detalhes. Tenho que concordar, porém a característica marcante que é elogiada no meio corporativo das fábricas de automóveis é a qualidade de suas carrocerias em termos de forma e função. Na realidade, a Mercedes-Benz sabe fazer carrocerias como ninguém. E esta característica vem de longa data.
Por exemplo, em 1949 as carrocerias já eram projetadas para que as portas não se abrissem espontaneamente em caso de acidente. Em 1951, as zonas de deformação progressiva das carrocerias, incluindo a rígida célula de sobrevivência, já eram consideradas no projeto. Em 1958, as carrocerias já eram submetidas a rigorosas especificações para impacto frontal e lateral.
Em 1973 a Mercedes-Benz adotava o teste de impacto parcialmente deslocado contra barreira indeformável, simulando a concentração dos esforços solicitantes em colisão frontal parcial, típica de quando um carro desgarra numa curva à direita (em países de mão direita) e colide contra um que vem pela pista contrária; a batida neste caso não é totalmente de frente .
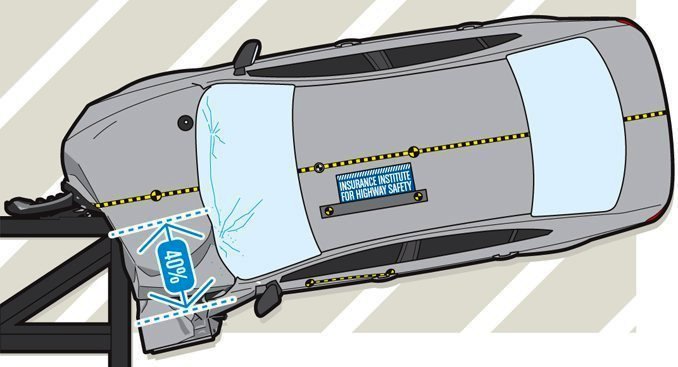
E como é difícil executar a engenharia de projeto de carrocerias, onde existe sempre o compromisso fundamental de forma e função! Deve agradar em estilo, suportar os esforços solicitantes em todas as situações de rodagem e também atender as características de segurança em testes homologatórios de impacto. Se hoje nas análise virtuais com auxílio de poderosos softwares já é complicado, imagine na época em que os projetos eram todos calculados “na mão limpa”, somente com o conhecimento puro do engenheiro.
Um bom exemplo de eficiente calculo estrutural, foi desenvolvido no início da década de 1950, o Mercedes-Benz 300 SL. Todo treliçado, com os elementos trabalhando em tração e compressão, tinha uma estrutura brilhante nos modos de flexão e torção de sua carroceria.
Veja o leitor, além da estrutura treliçada, a viga transversal (cross car beam) que se integra com a parede de fogo e apóia a coluna de direção.
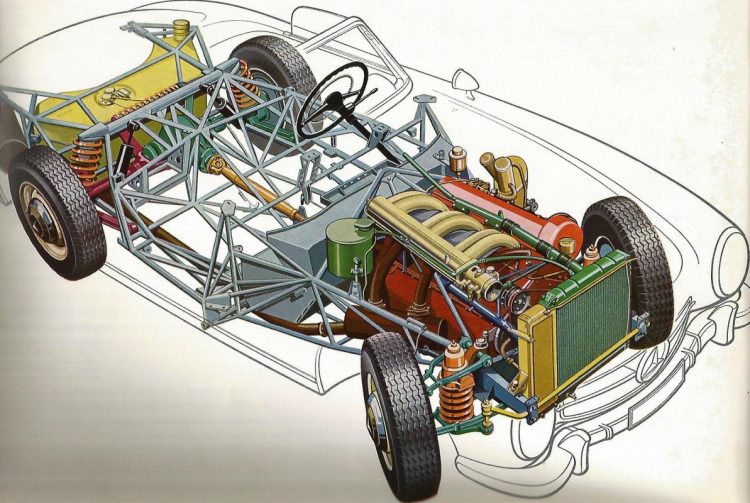
Alguns modelos virtuais/estruturais de hoje em dia também simulam integração de treliças e calculam pontualmente, com muita precisão, o nível de tensões solicitantes ao longo de toda a carroceria.
Outros modelos de cálculo dividem a carroceria em elementos previamente escolhidos pelo próprio software e calculam também pontualmente o nível de tensões de compressão, tração e cisalhamento ao longo de toda a carroceria. Áreas críticas são recalculadas a partir de detalhes específicos para adequação do coeficiente de segurança aplicado.
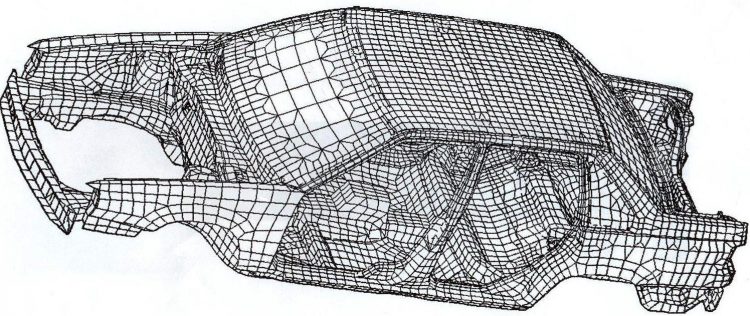
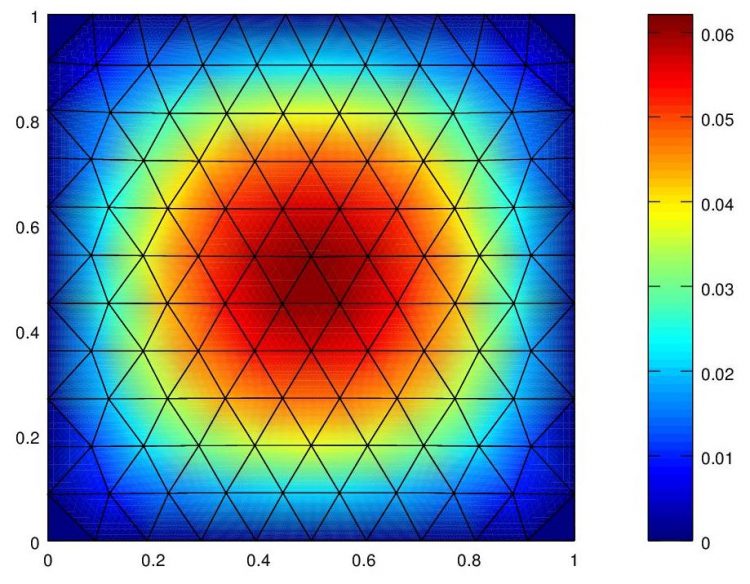
No inicio da década de 1990 a Mercedes-Benz adotava menos vincos estruturais e chapas com diversas espessuras e/ou aços com várias composições, principalmente na estrutura interna, não visível.
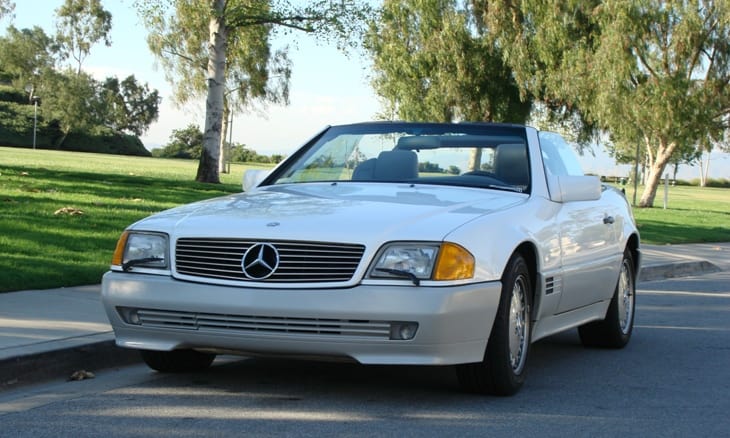
A Mercedes-Benz continua a sua saga de manter o desenvolvimento de suas carrocerias sempre um passo à frente, utilizando testes laboratoriais, cálculos estruturais e comprovação em protótipos. Aliás, os laboratórios de testes estruturais da Mercedes-Benz são padrão de referência para a indústria, tanto para carros quanto para caminhões. Outra empresa que também está se dedicando muito neste aspecto é a Volkswagen, inclusive no Brasil, investindo cada vez mais neste tripé de desenvolvimento.
Falando em eficiência de forma e função, vem-me à cabeça o Mercedes-Benz SLK, modelo lançado em 2010 que associa vincos de caráter estrutural se integrando perfeitamente com as belas linhas do veículo.
Chamo a atenção para o fato de que os veículos conversíveis da Mercedes, de maneira geral, sofrem menos da “dança do pára-brisa” (cowl shake), que é aquela oscilação lateral do pára-brisa e do espelho interno que tanto incomoda os ocupantes do veículo. “Cowl”, cobertura em inglês, não tem tradução exata nessa aplicação, mas é a parte da carroceria que sustenta o pára-brisa e o capô. No Brasil, os funileiros (ou lanterneiros) chamam essa parte do carro, o cowl, de torpedo.
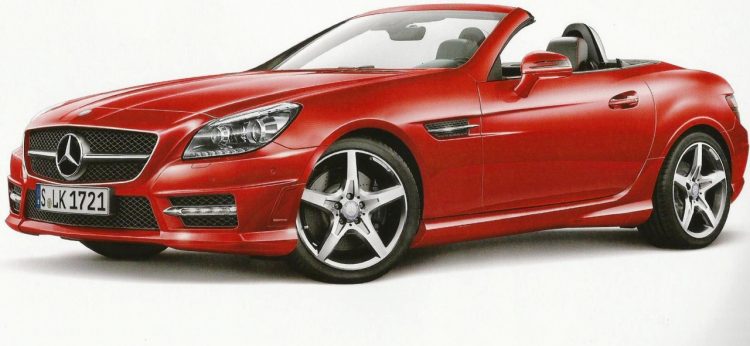
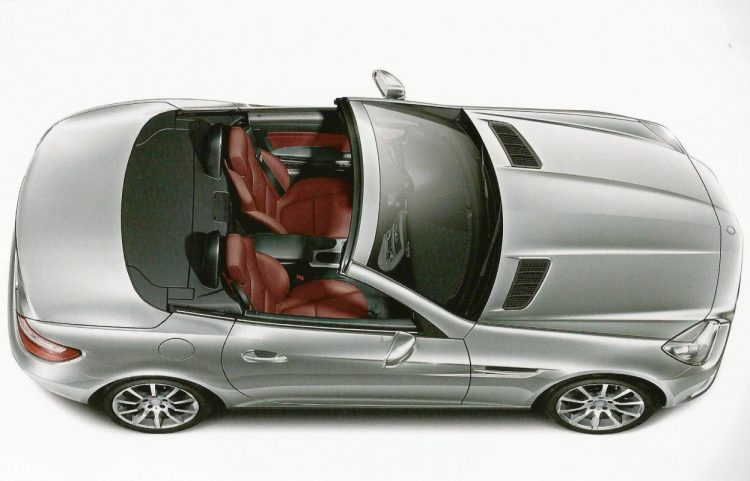
Como presente ao leitor, anexo duas fotos do elegante painel de instrumentos do SLK.
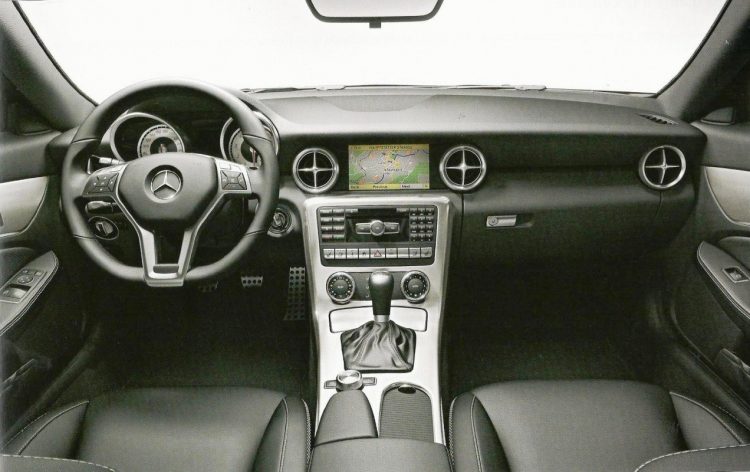
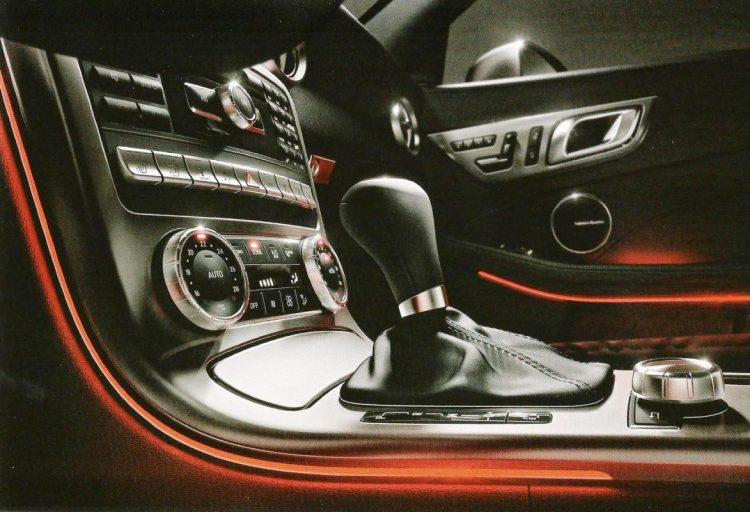
Como sempre encerro a matéria com uma homenagem. Desta vez vai para o leitor do AUTOentusiastas que ao longo dos anos vem colaborando com seus comentários, sempre agregando valor às matérias.
CM