A boa imagem que um veículo transmite ao consumidor depende de vários aspectos, sendo os principais sua resistência a falhas e a facilidade e custos de manutenção. Nada se compara à decepção do dono ficar na mão, principalmente se for um carro novinho em folha.
Com essa matéria, quero dar ao leitor ou leitora uma ideia do se faz num fabricante para que a experiência de possuir um carro seja a mais prazerosa e livre de problemas possível.
Problemas de projeto são mais raros de acontecer, porem quando acontecem é recall na certa.. Na verdade, a maioria das falhas que acontece nos automóveis é resultante da qualidade dos processos de fabricação, podendo também estar relacionados com projetos complicados, de difícil execução e controle de manufatura.
Já foi o tempo em que as revendas e oficinas autorizadas da marca eram verdadeiras salas de visita, mantendo estoque de componentes e serviços disponíveis a qualquer hora. Hoje em dia, peças somente por encomenda, serviços somente com agenda marcada e o consumidor que se vire.
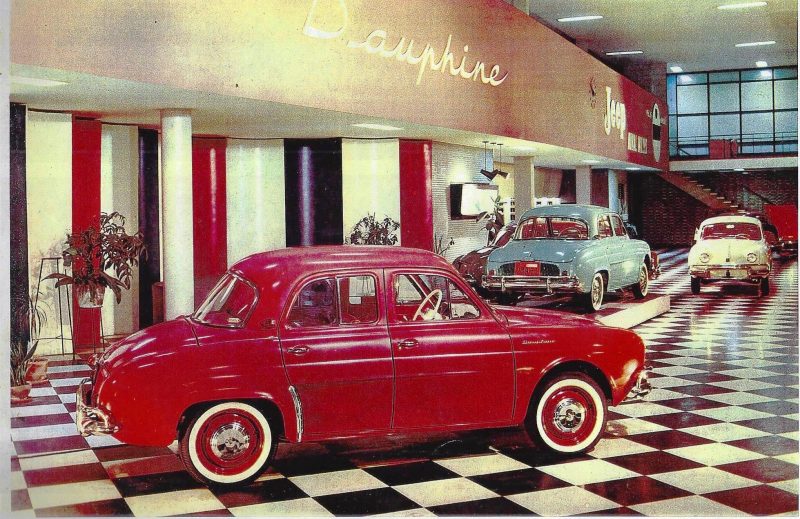
Cada fabricante estabelece uma expectativa de durabilidade para os seus veículos, tendo por base suas aplicações, uso urbano, uso misto, fora de estrada, etc. O primeiro passo é saber em qual mercado o veículo será comercializado, pois cada mercado tem suas particularidades em termos climáticos e condições de rodagem, rodovias, buracos, estradas de terra, estradas de cascalho, pavimento quebrado, lombadas, valetas, etc.
Hoje em dia, com os veículos se tornando cada vez mais mundiais, o mercado mais severo tende a ser a base para o projeto, com ênfase a evitar duplicação de componentes. A maioria das fabricas, para não dizer, sua totalidade, já possui varias rotas de teste correlacionadas em seus campos de prova, representando o mundo real de utilização do automóvel. As rotas correlacionadas são definidas a partir de uma rota real que represente a utilização do veículo com índice de confiabilidade maior que 90%, representando os circuitos de cidade, rodovias, estradas secundárias, terra, pedrisco e todas as situações características do mercado.
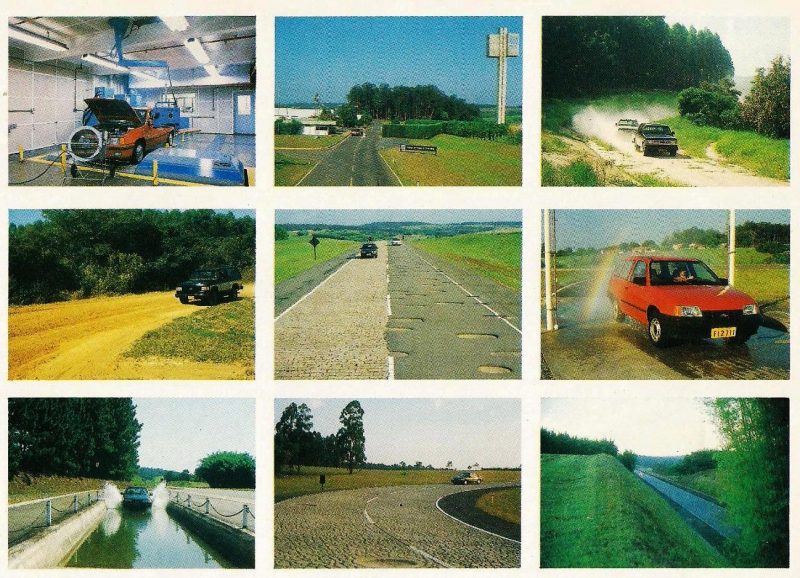
Um veículo de teste é totalmente instrumentado para monitorar a rota em questão com resultado em tempo real das solicitações nas rodas, esforços no volante de direção, número de aplicações dos pedais do freio e embreagem, posições do pedal do acelerador e também todos os seus esforços operacionais, além das temperaturas do motor e transmissão, trocas de marcha, condições ambientais e carga, torque, potência, acelerações e desacelerações, tempo em marcha-lenta, etc.
A título de curiosidade, a VW do Brasil,na década de 1980, definia uma rota real e cumpria 100.000 km para entender a durabilidade geral do veículo. Testes em laboratório complementavam as informações. Na mesma época, a Ford do Brasil, com seu campo de provas, definia suas rotas correlacionadas equivalentes a 160.000 km no mundo real.
Testes em laboratório de estrutura são comuns hoje em dia, simulando os esforços solicitantes em três eixos, vertical, longitudinal e transversal. Processo que facilita análises de componentes e melhorias no conjunto, testando com precisão varias peças com modificações de engenharia.
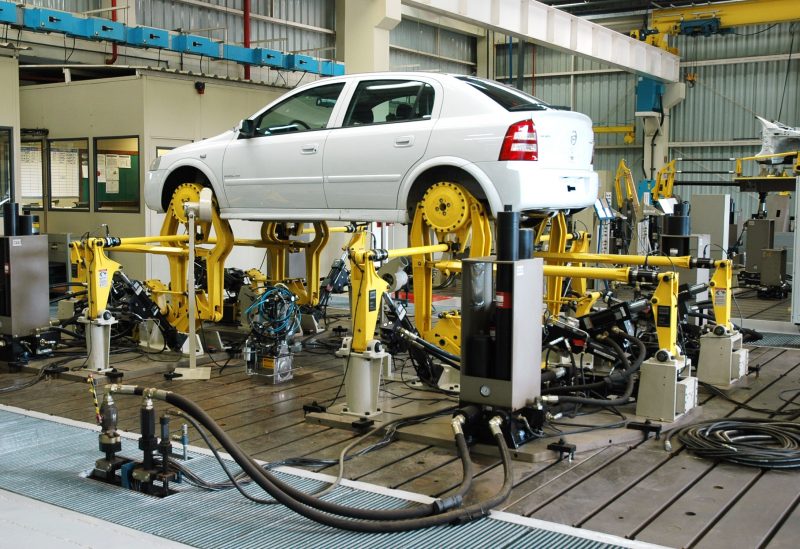
Os projetos são direcionados estabelecendo um coeficiente de segurança que leva em conta a durabilidade e o custo envolvido. De maneira geral, quanto maior o coeficiente de segurança adotado, tanto maior será o custo do veículo. A escolha do ponto de equilíbrio entre durabilidade e custos é por definição responsabilidade do corpo diretivo da empresa.
É importante que se diga que os sistemas críticos que envolvem a segurança , suspensão, freio e direção, são tratados de maneira especial. A regra é que os componentes devem alertar quando alguma coisa vai mal, através de ruídos, vibrações, folgas e trepidações sentidas na carroceria e particularmente no volante de direção. Também a instabilidade direcional, perda de eficiência e aumento dos esforços operacionais fazem com que o motorista perceba um possível problema e procure uma oficina com urgência, antecipando a correção de uma falha.
Outro ponto fundamental é que em caso de fortes impactos em buracos, por exemplo, não pode haver quebra fácil, por fragilidade, de nenhum componente que ponha em risco a segurança do veículo. Deformações são permitidas dentro de um nível estabelecido em testes específicos pela engenharia.
A grande vantagem dos campos de provas é permitir a repetibilidade dos testes de modo a identificar possíveis anormalidades de projeto e de qualidade interna e dos fornecedores, comparativamente. Todos os sistemas mecânicos, elétricos e cosméticos de acabamento são testados e avaliados.
Também são executados os testes e ensaios homologatórios exigidos por lei, como os de segurança em barreira de impacto e freios, e os ambientais de emissões de gases poluentes e ruído.
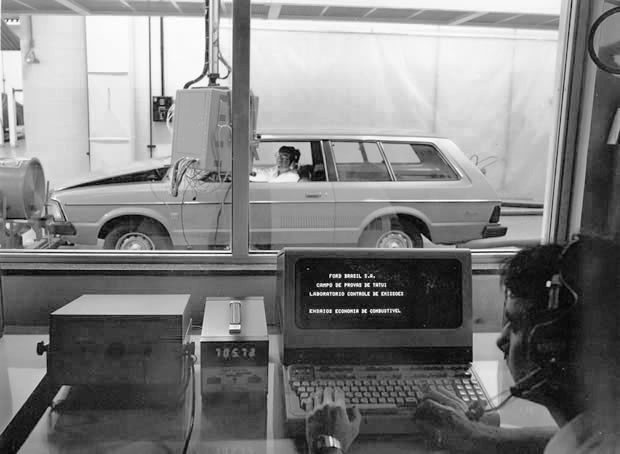
Peças de acabamento em plástico, tecido e pintura são submetidas a testes de exposição solar e raio ultravioleta.
Sistemas de embreagem são testados em partida em rampas e também em testes severos de impacto nas trocas rápidas de marcha.
Os veículos são é submetido também a testes severos de estanqueidade, entrada de água e poeira. O teste de poeira é normalmente efetuado em circuito fechado, onde o carro da frente levanta forte nuvem de poeira para o carro de trás. O teste de penetração de água é feito em chuveiros e também em passagem por alagados.
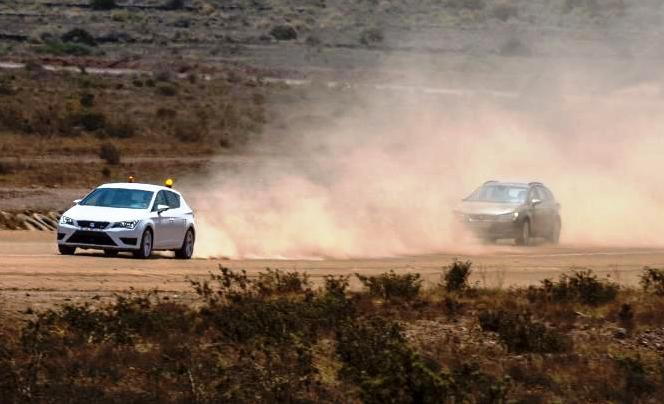
Testes em câmaras especiais com névoa salina determinam a vida da carroceria e componentes. A severidade deste teste é bem relevante, facilitando a identificação de componentes não protegidos contra a corrosão. Imagine, névoa salina quente agindo em todo o veículo.
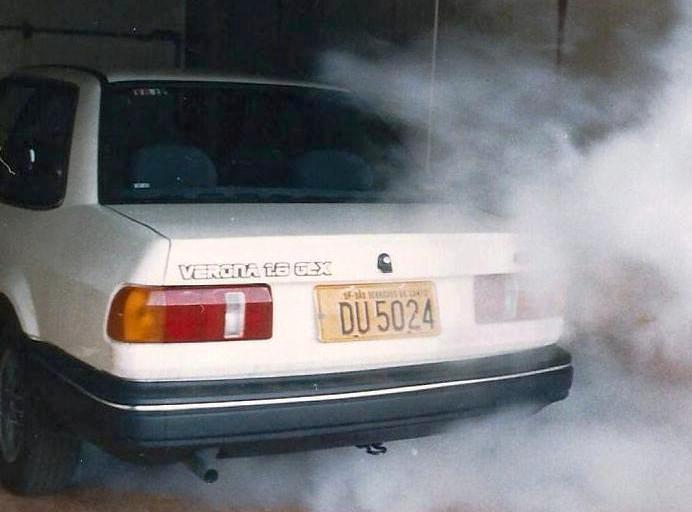
Os contatos elétricos também são avaliados, com atenção especial em termos de eficiência quanto à corrosão. Hoje em dia os projetos estão contemplando contatos de latão com acabamento em prata e até em ouro para evitar panes elétricas que podem afetar diretamente a segurança do veículo, por exemplo, o motor apagar durante uma ultrapassagem.
Interferências de tubulações de combustível, chicotes elétricos, tubulações de freio que possam desgastar e falhar são meticulosamente avaliados e testados.
Interferência eletromagnética sobre os equipamentos eletrônicos, como o módulo de gerenciamento dos motores são testadas em laboratório.
Riscos de incêndio são amplamente avaliados e testados em programas de modos de falha para garantir em 100% a integridade dos componentes e a segurança.
Outro ponto fundamental, que nenhum processo virtual pode substituir, é a interação de todos os sistemas e componentes do veículo que é realizado por engenheiros especialistas, que avaliam e ponderam todas as variáveis para que o veículo seja coerente em todas as suas funções.
Em resumo, cada fabricante tem um critério próprio para estabelecer a vida útil de seus veículos, com base em correlações de rotas reais com os testes em laboratórios e campos de provas. Quanto maior o coeficiente de segurança adotado, tanto maior o custo envolvido, requerendo a utilização de materiais mais nobres, sistemas de projeto mais sofisticados, manufatura com controles mais rigorosos de folgas e ajustes e outros cuidados. Cada caso é um caso e cada fábrica é uma fábrica.
Obviamente que o consumidor tem papel relevante na durabilidade de seu veículo, fazendo as manutenções periódicas e limpeza do exterior e interior.
Encerro esta matéria com uma homenagem à Ford Motor Company Brasil e seu Campo de Provas em Tatuí, no interior de São Paulo.
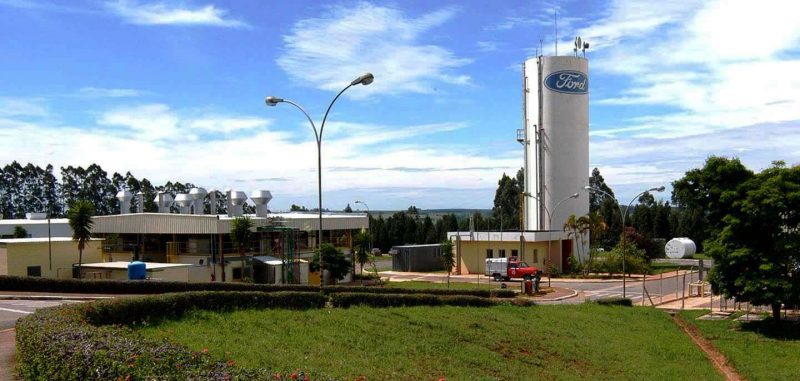
CM