A indústria automobilística brasileira, de forma geral, perdeu muita força nos últimos trinta anos. Até então, algumas empresas puramente nacionais conseguiam sobreviver em meio às gigantes multinacionais, mesmo com baixo volume de vendas. Hoje em dia, não há mais nenhuma fábrica nacional que não seja de réplicas que tenha sobrevivido por conta própria.
O motivo é de certa forma simples. Dinheiro. Nada mais que dinheiro, ou no caso, a falta dele. Nunca foi barato fabricar automóveis, mas nos dias de hoje, está muito pior. Para simplificar um pouco, nem vamos entrar no mérito das últimas exigências legais que custam uma boa grana, como o ABS e o airbag.
Muitos visionários com bases sólidas e também muitos aventureiros desavisados tentaram fabricar automóveis no Brasil, e podemos contar nos dedos quanto tiveram algum sucesso. Uma coisa muito importante é posicionar os fabricantes no tempo, pois cada época da história tinha suas peculiaridades, a favor ou contra os empreendedores brasileiros.
As dificuldades são sempre as mesmas. Em primeiro lugar, acertar o nicho de mercado do produto a ser criado. Não adianta tentar vender gelo no Polo Norte, tem que vender sorvete na praia. Muitas vezes bons carros são criados, mas estão deslocados do que o mercado quer, ou aceita pagar. Boa parte dos que querem fazer um carro nacional pensam em fazer esportivos. Todo mundo gosta de esportivos, são sonhos de consumo de todo o entusiasta. Mas, infelizmente, bem poucos são reais compradores. Não é um mercado de escala no Brasil.
O custo de fabricação é o segundo problema, e é o que mata 90% dos projetos. Para se ter um custo mais baixo, é preciso ter volume. Se o volume aumenta, os custos caem, pois a produção seriada melhora o rendimento do processo produtivo. Porém, para se ter um volume alto, é preciso ter grande demanda, o que nos leva de volta ao problema número um do mercado. É um ciclo vicioso.
Vamos entender porque os custos são altos. Novamente, é diretamente proporcional ao volume desejado. Para se ter um grande volume de produção, o investimento requerido é muito grande, e praticamente ninguém tem o suficiente para investir. Imagine gastar mais ou menos R$ 150 mil só para desenvolver uma manga de eixo, ou R$ 500 mil só para fazer uma barra estabilizadora. Um motor ou transmissão, nem pensar. Fazer um carro só é fácil, o problema é fazer 200 ou 500 iguais.
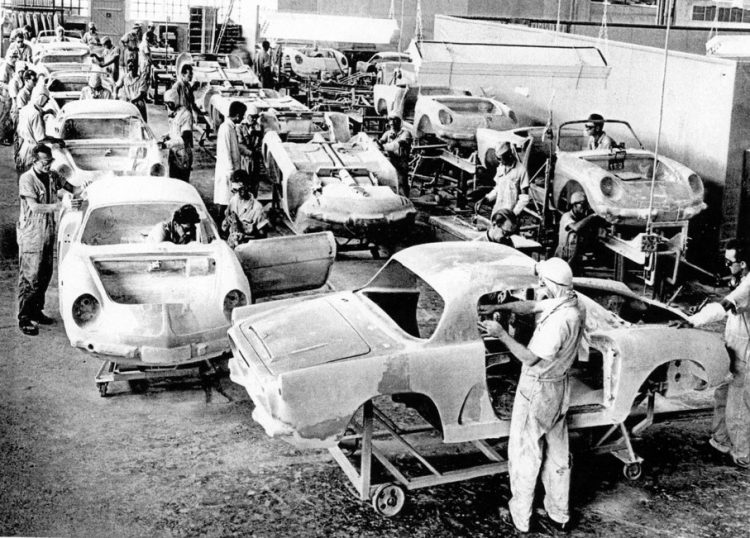
O investimento em cada componente do carro é alto pois requer moldes, ferramentas, dispositivos de fabricação e de medição, pinturas, embalagens, montagens e até mesmo manuseio das peças, tudo para que se consiga peças iguais e intercambiáveis, que é a base da produção em série. A indústria de autopeças fornece para grandes fabricantes volumes muito altos, e o tempo e espaço na fábrica para que forneçam pequenas quantidades a outros fabricantes menores custa caro. Com investimentos limitados, criar peças próprias fica quase que inviável, e ai começa a operação de caçador. Isso mesmo, caçador, porque é como uma caçada às peças já existentes de mercado e que podem servir ao projeto. Este fator, por si só, já prejudica brutalmente a criação de um projeto nacional. O próprio público cria uma barreira mal fundamentada, só com comentários como “olha, é o painel do Palio”, “é o botão do vidro do Corsa” ou “já vi essa maçaneta num Gol”.
Não há problema algum em usar peças de outros carros. Já estão prontas, desenvolvidas, ferramental pago e certificadas, basta escolher corretamente e com critérios embasados em boa engenharia para não sair pegando qualquer peça por ai. Se possível, usar as peças existentes em pontos que não são tão visíveis ao usuário, ou trabalhar na sua aparência para que não fique muito evidente que veio de outro carro.
Quando trabalhei na engenharia da Lobini, a grande dificuldade era conseguir o volume de peças desejado a um preço competitivo. O carro era caro pois os componentes eram caros. Muita coisa era importada. Como a demanda era pequena, o custo das peças de baixo volume era elevado. Muitas peças eram feitas nos fornecedores em linhas especiais e com processo de protótipos, manualmente e sem o uso de ferramentais, processo este normalmente usado para criar as primeiras peças de teste antes de se iniciar a produção em larga escala nos ferramentais definitivos.
Muitos fornecedores nem aceitavam fabricar peças para os primeiros teste, pois não seria de interesse deles iniciar uma produção de peças mensal que não chegaria nem de longe a um décimo do volume normal da sua produção corrente. Não era interessante financeiramente para eles.
Itens importantes para atender os requisitos de projeto geralmente não podem ser reutilizados de outros carros. Por exemplo, para um carro esporte onde o comportamento dinâmico é primordial, braços de suspensão e mangas de eixos em geral precisam ser exclusivos para que a correta geometria de suspensão seja criada. Isto já gera um custo diferenciado, pois peças novas terão que ser fabricadas, na própria fábrica ou em fornecedores externos, que podem não aceitar em função do baixo volume, ou cobrar bem caro para fabricá-las.
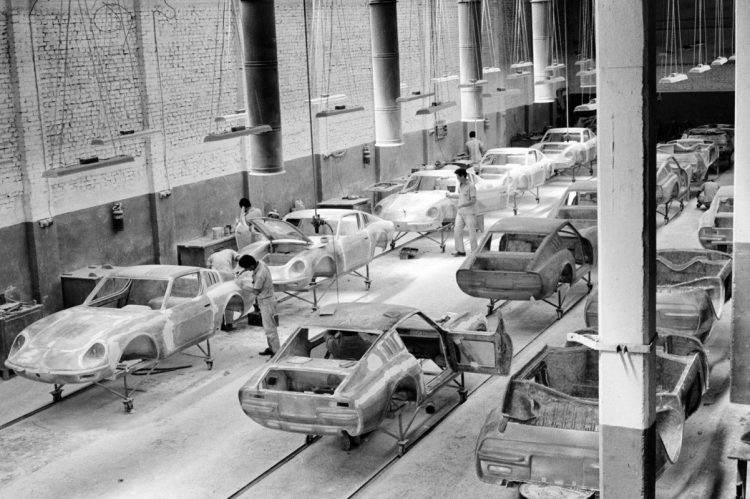
Peças de carroceria também são exclusivas e requerem ferramentais para fabricação. Se for de aço, o custo é altíssimo pois requer grandes prensas e moldes complexos. Se for compósito dede fibra de carbono, também requer equipamentos especiais como uma autoclave para ser bem feito, além do elevado custo de matéria-prima e o conhecimento necessário poucos possuem. Se for compósito de fibra de vidro, é bem mais barato, mas a dificuldade do processo artesanal de pequena escala aumenta o preço, além do fato de ainda haver discriminação com esse material no Brasil. O processo da Lobini era extremamente artesanal, havia ainda possibilidade de aprimorar para ganhar em velocidade de fabricação, o que poderia baixar um pouco o custo da carroceria e montagem.
Veja bem, estamos até então falando de componentes simples (exceto a parte da carroceria), como suportes, braços e pequenas peças usinadas. Quando falamos de itens maiores e de maior valor agregado, como o conjunto motor e transmissão, não tem como escapar. Vai ter que ser comprado de um grande fabricante, e é nesta hora que a balança pende para o lado errado.
É muito difícíl um grande fabricante, hoje em dia, aceitar vender componentes para uma outra fábrica independente a um preço baixo aqui no Brasil. Vender então a preço de custo, nem pensar. Mesmo com um contrato de fornecimento direto assinado, o valor cobrado ainda é alto e impede que se tenha uma estrutura de custos enxuta. O pequeno fabricante também fica dependente do que acontece no fornecedor. Se cancelarem uma peça, não vai ter o que se fazer, o projeto tem que mudar para se adequar ao que o mercado oferece.
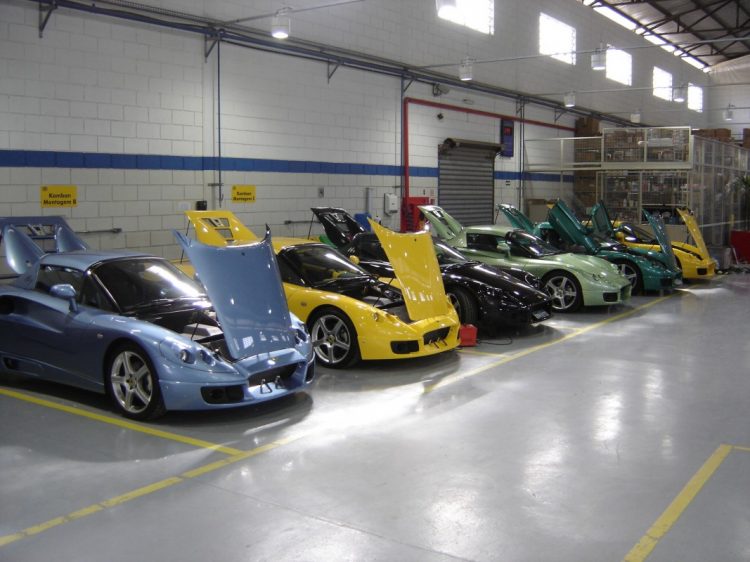
A dependência e interligação de sistemas eletrônicos hoje é outro complicador e agregador de custo. Antigamente era bem mais simples. Um motor para funcionar precisava apenas de combustível no carburador, um cabo de acelerador, uma bateria e um alternador. Hoje, com diversos sistemas eletrônicos de comando, há inúmeros chicotes, sensores e cabos, tudo interligado com centrais eletrônicas, com o painel e até com a chave de partida codificada.
Eliminar toda esta dependência eletrônica sem ser em um projeto de sistema específico é muito difícil e ficaria muito caro. Desenvolver uma central eletrônica própria custa uma fortuna, e ainda há o complicador das normas de emissões de poluentes que dependem da calibração do motor, cada vez mais restritas e exigentes.
A melhor forma é utilizar o conjunto completo de um único carro, como é o Lobini H1. Motor, transmissão, central eletrônica, chave e painel originais de um único “doador”. A única coisa que precisa ser feita especialmente para o carro é o chicote elétrico, que já é um problema considerável. Veja que voltamos ao problema do preconceito da salada de peças de outros carros junto com o problema de achar um fornecedor que aceite fabricar um chicote especial a um custo razoável.
O leitor pode lembrar que muitos pequenos fabricantes nacionais tiveram sucesso por um tempo, como a Puma, Gurgel e MP Lafer. Na época de cada um destes, as condições de fornecimento de peças eram outras. A Puma conseguia, por exemplo, comprar motores e muito componentes direto da VW a um custo baixo. A complexidade do carro era bem menor, o processo montado na fábrica da Puma era bem feito para sua demanda, e o equilíbrio financeiro manteve-se positivo por muitos anos.
Com o passar dos anos, os acordos foram mudando, as pessoas que tinham interesse em manter a relação Puma-VW foram deixando seus cargos, e cada vez mais era difícil manter o equilíbrio, até o ponto em que o custo tornou-se um problema. A demanda do mercado também mudou ao longo dos anos.
O que falta são parceiros comerciais interessados em contribuir com a indústria nacional, que topem fornecer peças de baixo volume a um custo razoável. Economicamente é muito complicado, acaba dependendo do interesse em contribuir acima o lucro financeiro. Não vou dizer que não existem tais interessados, pois não seria verdade. Tínhamos alguns destes fornecendo peças para a Lobini, e muitos outros se mostraram interessados em fazer parte de um projeto nacional apenas pelo fato de estarem apoiando um desenvolvimento local de um produto diferenciado, no caso um esportivo que atrai olhares.
Hoje temos a Troller como uma das mais bem-sucedidas empresas nacionais, mesmo estando atualmente debaixo de uma multinacional. Quando ainda era independente, a estrutura montada e os processos de fabricação foram muito bem planejados para manter o produto viável, mesmo não sendo um veículo barato em termos absolutos. Eles acertaram o nicho de mercado e conseguiram parceiros para viabilizar o projeto. Também tiveram dificuldades ao longo do projeto para ter os componentes apropriados, mas conseguiram se estruturar.
Associando todos estes fatores, podemos entender um pouco melhor porque é tão caro fabricar um automóvel em série, principalmente no Brasil. A dependência dos fornecedores é crucial, e quase sempre não é possível chegar ao equilíbrio de interesses das duas partes. Não é cultura industrial nossa, ao contrário, por exemplo, da Inglaterra, onde diversos pequenos fabricantes sobrevivem com a ajuda das grandes marcas.
Para os carros esporte nacionais, se houvesse uma demanda maior, os investimentos poderiam ser melhor justificados e até mesmo conseguir parceiros comerciais que viabilizassem a criação de uma fábrica apropriada para o mercado nacional. Para piorar, não há incentivo adequado do governo em fortalecer as pequenas indústrias locais, algo que teria um grande impacto nos custos.
Esta condição de difícil fornecimento e mercado reduzido está cada vez pior, o que nos leva a cada vez menos empreendedores arriscando novas ideias e investimentos. É uma pena, pois diversos bons projetos nem conseguem sair do papel, e nada indica que o cenário atual vá melhorar.
MB